Development of a sensor system and a multi-channel measuring device for simultaneous measurement of soil pressure and deformation
In the first project phase, the scientists developed the SoilAssist sensor system (SASS). It enables the derivation of various machine data or tire data. Another result is a multi-channel measuring device for the simultaneous measurement of soil pressure and ground and deformation at different soil depths. In the second project phase, the focus is on further development and improvement of the SASS and field measurements with both systems.
Further information and results of the SASS and the multi-channel measuring device can be found here.
SASS ...
With the innovative SoilAssist sensor system developed in the first phase of the project, machine data and information on the tire-soil interface can be derived.
The SASS developed in the first project phase enables the derivation of machine data, tire data and information on the tire-soil interface (e.g. contact area pressure, track depth), which can be linked to changes in soil functionality in the topsoil and subsoil by measuring (multi-channel measuring device) or modeling (soil pressure and deformation model) soil pressure and deformation.
The SASS measures and monitors the dynamic wheel load, tire inflation pressure, contact area, contact area pressure, and track depth of agricultural machinery in real time. It consists of an ultrasonic sensor for measuring tire deflection and a pressure sensor for measuring the tire inflation pressure. The sensors are mounted in each tire rim of the machine. In addition, an ultrasonic sensor is located under each axle to measure the track depth.
The transmission of the sensor data to the central tablet PC on the machine in the driver's cab was realized via WLAN. In addition, the correlation of sensor data and wheel load, contact area and contact area pressure for different tires was determined at the tire test stand of the Institute of Agricultural Technology and in the field as a function of tire dimension and tire inflation pressure. These relationships were integrated into the graphical user interface of the adaptive assistance system of the project partner DFKI on the tablet PC. This enables the on-board assistance system to dynamically derive the contact area pressure under each individual tire in real-time in field traffic. The system is thus able to dynamically provide information about the current soil load. This is a prerequisite for modelling the effects on soil parameters and functions and for deriving recommendations for optimizing machine parameters and driving routes.
The scientists carried out measurements with the SASS in the 1st and 2nd project phase on the New Holland measuring tractor and the Grimme beet harvester. As a result, we were able to show, for example, the different loads on the headland during soil cultivation with a cultivator between lifted and trailed cultivator. When the cultivator is lifted, it is attached to the tractor's three-point hydraulic. At the headland, the cultivator is lifted so that its entire weight rests on the rear axle of the tractor. With this additional weight it drives over the headland when turning. With the device attached, the cultivator is raised hydraulically out of the soil via a roller on the headland. As a result, the weight on the rear axle of the tractor hardly changes when driving over the headland. The rear axle of the tractor with attached cultivator has a load similar to the value received by static weighing (approximately 4.7 t). The load increases to approximately 6.5 - 7.0 t when the cultivator is lifted. This means a difference of about 2 t, which is additionally applied to the headland when the cultivator is lifted.
It is clear from the investigations that the choice of the respective cultivation technique can have a considerable influence on the load distribution in the area. This is countered by the fact that the trailed cultivator is more expensive and requires additional investment costs. The socio-economic subproject investigates a medium to long-term amortization of the additional costs. For increasing soil protection and improving soil functions we recommend using trailed implements.
Multi-channel measuring device
With the multi-channel measuring device it is possible to simultaneously measure soil pressure and deformation caused by wheeling of agricultural vehicles at different soil depths.
The scientists developed a multi-channel measuring device for the simultaneous measurement of soil pressure and deformation at different depths. With this device, the propagation of pressure and deformation caused by agricultural field traffic can be tracked from the soil-tire interface down to deeper soil layers. Dynamic driving effects are shown with in-situ measurements. The measurement of soil pressure using Bolling probes provides information on the pressure distribution in the soil due to mechanical load inputs (Bolling, 1987; Lebert, 2010). By means of soil pressure measurement in combination with the determination of the contact area pressure, the load on the soil can thus be determined at different depths. However, this value does not initially say anything about the effects on soil functions or structural changes in the soil. Therefore soil structural changes in the soil must be measured simultaneously.
Changes in the soil due to driving is the deformation of the soil. As long as this occurs elastically and the soil springs back to its original state, it can be assumed that its properties have not changed. However, if plastic deformation processes occur, the functional changes of the soil must also be recorded. For this reason, a system has been developed in SoilAssist that is based on the measuring principle of a hydrostatic measurement hoses and is capable of measuring deformations in the form of height differences with an accuracy of 0.1 mm. The deformation measurement indicates both a soil structural change and whether compaction is elastic or plastic. It is not possible to make a statement about harmful compaction that affects the functionality of the soil structure with this method alone, but it can be determined whether the traffic has contributed to a deterioration of the initial state. These measurements are combined with results from undisturbed soil sampling at different soil depths to determine changes in soil structure and functions caused by driving on the soil.
In addition to nine Bolling probes for soil pressure measurement, the multi-channel measuring device consists of nine deformation measuring probes for measuring soil deformation at three depths in triple repetition. A "Pressure and Deformation" software program was developed for field measurement and recording of the pressure and deformation data. It serves to visualize and record the measurement signals supplied by the soil pressure and deformation sensors.
The deformation measuring hoses and the Bolling probes of the multi-channel measuring device are inserted for the wheeling tests in a laterally located, prepared soil pit from depths of 20, 35, and 50 cm directly under the tramline. For the wheeling test, the agricultural vehicle passes the measuring point so that the sensors can measure directly below the center of the tire.
Results of different agricultural machines on ground pressure and settlement can be found here.
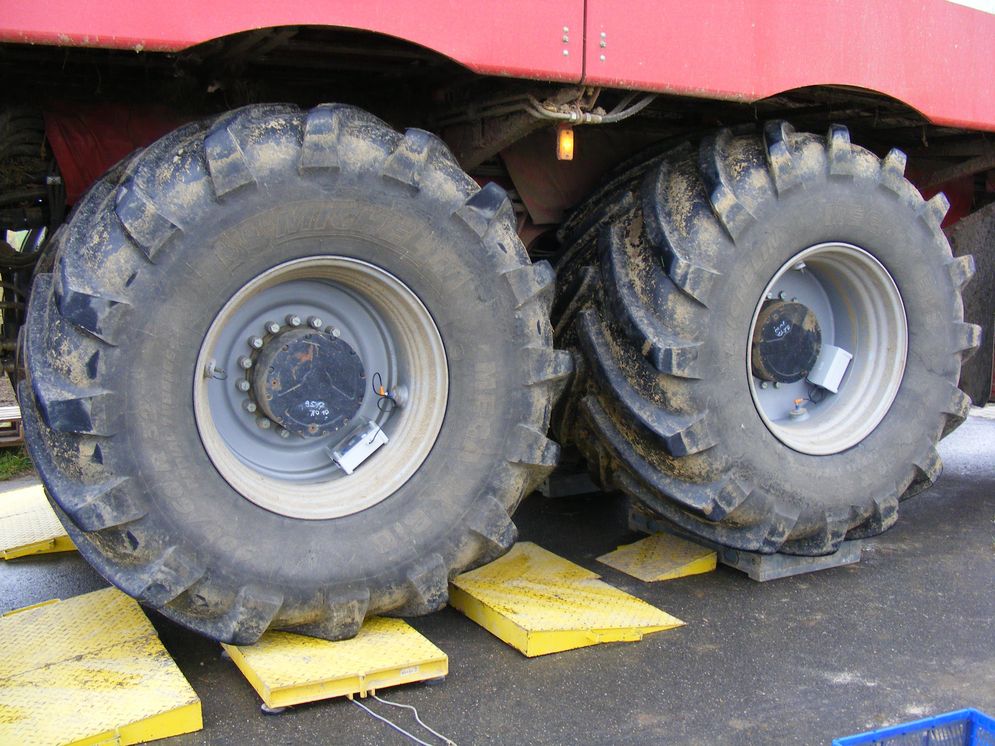